How Contactors Work: The Basics of Motor Control and Protection
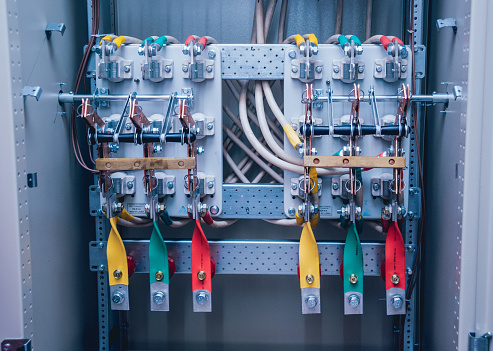
Have you ever thought about how your daily use appliances, like lights, fans, pumps, and other electrical machinery, work? What is the component responsible for their work? The answer is – Electric Motors.
Electric motors are employed in applications for running household appliances to power industrial machinery. And it is crucial to control and protect these electric motors. Now, who will do that? Motors have a complex system of components and circuits to maintain and protect them; that’s where contactors come in.
In this blog, we will analyse Motor Control and Protection and examine the role of contractors. We will also discuss the working principle and types of contactors so that you can gain a deeper understanding of them. Follow us on this blog as we explore it in great detail.
Before moving towards contactors, we need to understand the basics of motor control and protection.
Understanding Motor Control and Protection
Motor Control Basics: An electric motor has two primary components – the stator and the rotator. The stator is a stationary component that has coils. The rotator is a rotating part that has conductors in it. A magnetic field is created when the current flows through the coils in the stator. It interacts with conductors in the rotators, causing the rotatory motion.
To handle the direction and speed of the motor, we need to control the amount and direction of current flowing through the coils. It is carried out by a motor controller, combining switches, relays and contactors.
Motor Protection Basics: The motor needs protection from damage due to overcurrent, short circuits, and other electric faults. You can protect motors by using a combination of fuses, circuit breakers, and overload relays. Fuses and breakers protect the motor against short circuits and overcurrent. Overload relays protect against thermal overload.
What are Contactors, and How Do They Work?
A contactor is an electrically controlled switch controlling the current flow to a motor. It has two primary components – a stationary contact and a moving contact. The stationary contact is connected to the power supply, and the moving contact to the electric motor.
Contactors work on the principle of Electromagnetism. When the current flows through the coil, it creates a magnetic field. The magnetic field’s strength depends on the current flowing through the coil, controlled by the control circuit.
When the contactor is energised, it attracts the moving contact towards the stationary one. It closes the circuit, which allows current to flow to the motor. When de-energised, the moving contact moves away from the stationary contact. It breaks the circuit and stops the current flow to the motor.
Some Common Types of Contactors
- AC Contactors: These contactors are engineered for use with AC motors. Depending on the application, they are rated for voltages of up to 600V (24V, 120V, or 240V) and currents of up to several hundred amps.
- DC contactors: They are used with DC motors and are rated for voltages similar to AC contactors and currents up to several hundred amps. These depend on the size and application.
- Definite Purpose Contactors: These are designed for specific applications, such as HVAC systems or refrigeration equipment.
- Reversing Contactors: These contactors control a motor’s rotational direction by reversing the current’s polarity flowing through the coils.
Ensuring Maximum Motor Control and Protection
Contactors are crucial for controlling the speed and direction of a motor to protect it against damage by electrical faults. Understanding the basics and working of contactors help us ensure the safe and reliable operation of electric motors in various applications. Throughout this blog, we covered everything from the basis of motor control and protection to the role of contactors in it.
Get the best-quality contactors for your motors and ensure efficient, effective, and reliable motor control systems.